
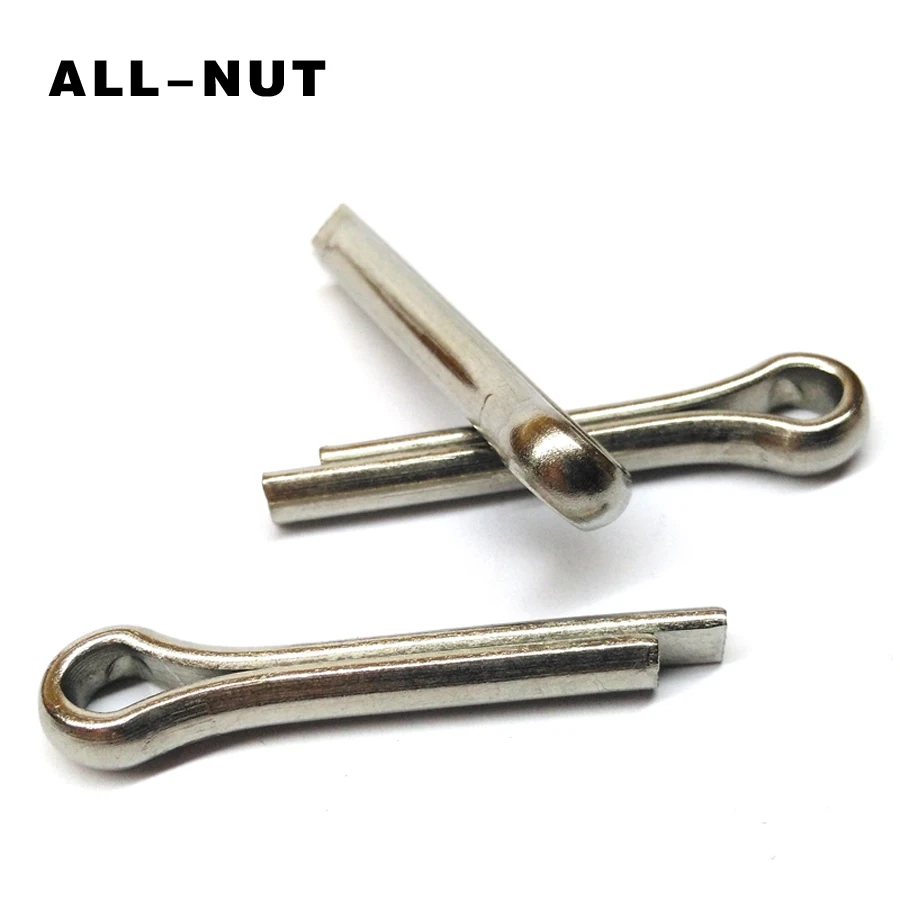
These pins are generally sold in packs of five. Our cotter pins are zinc plated and galvanised, making them particularly well suited to deployment outdoors, since they are capable of resisting corrosion and surviving in adverse conditions for extended periods. So whether you need five, ten or a whole kit consisting of a range of sizes, we will be able to meet your needs and supply you with affordable items of the highest quality. We stock a wide selection of split cotter pin products at Simply Bearings. It is always a good idea therefore to have a few spare pins to hand, so that replacement can be carried out swiftly, as and when needed. They act as an alternative to a staple, holding firmly in place using a pair of tines which need to be bent outwards to lock the pin in place.īecause of their design, a cotter pin that is removed after use needs to be replaced with a fresh pin. These pins are commonly used to secure castle nuts.Cotter pins can be an essential component in a range of mechanisms and scenarios, from ensuring that nuts remain tightly secured in place on shafts to keeping ramps in the correct position and allowing for ease of use when access is required. Hammerlock cotter pins are installed and locked in place with a hammer strike.
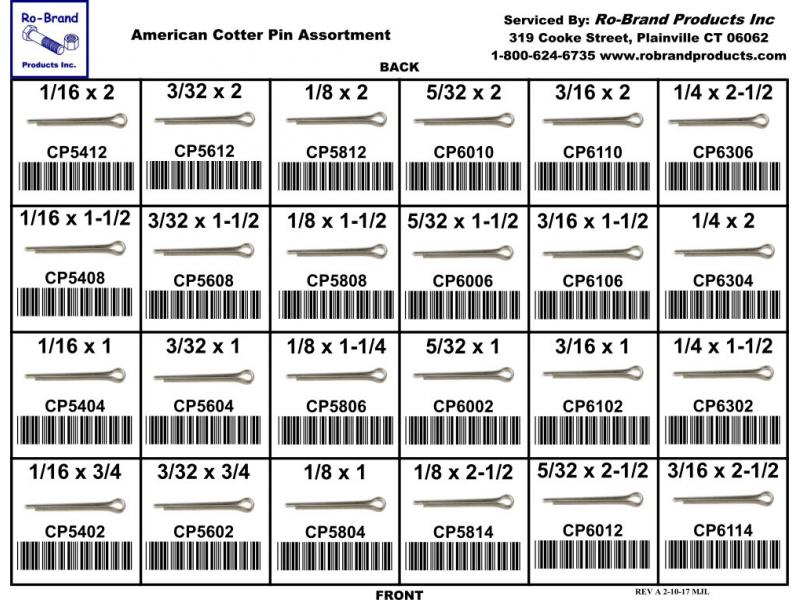
CircleĬircle cotters, or cotter rings, conceal sharp edges internally to protect materials such as fabrics that may be susceptible to damage. This design allows for a more securely locked assembly. Styleīow tie cotter pins feature a loop on both ends of the pin, allowing for push or pull installation from either side of a hole. It offers the highest strength compared to other metals and elements, but is the least corrosion resistant. The most common material used in fasteners, this material is predominantly iron mixed with carbon.
Cotter pins series#
There are over 150 grades of this material with the 304 and 316 series being the most common. The chromium forms a protective layer when exposed to oxygen, keeping the steel underneath from corroding. This material is known for its corrosion resistance and has varying strengths depending on the amount of chromium and nickel alloy. Stainless SteelĪn iron based material with a minimum of 10.5% chromium. Used in locks, gears, doorknobs, plumbing, electrical applications and musical instruments. It has excellent cold working (forming at room temperature) properties. As an electroplated finish it is nonmagnetic and resists corrosion well. This material has a distinctive bright golden coloring and is primarily used in aesthetic settings or in applications where low friction is necessary. This material has a general composition of 2/3 copper and 1/3 zinc. The corrosion resistance and ease of fabrication are why this grade is used in food industry machines, appliances, architectural trim and aquatic fasteners. The ASTM denotation for very similar grade is 304. It is comparable in strength to grade 2 materials, yet slightly weaker and easy to weld. A2-70Ī type of the most common stainless steel grade. The DIN/ISO denotation for a very similar grade is A4-70. It is used in more severe corrosive environments than 304 stainless steel, as such it is used in more industrial settings, like process chemicals, textiles, bleaches, salt water and rubber. It is on the low middle end of the grade scale. The second most common stainless steel grade, this material is stronger than grade 2, slightly weaker than grade 5,or generally as strong as medium to low carbon steel. This finish should not be used in marine or high salt spray environments. Slightly less corrosion resistant than yellow zinc, it is a versatile finish that is best used indoors. It is a popular finish because of its protection, value, and ease of coating. The zinc protects the steel from corrosion and the chromate layer protects the zinc from degrading. It is an electroplated zinc layer covered with a chromate post-treatment. This finish, also know as zinc plating, zinc chromate or dichromate provides good corrosion resistance and is the standard for many hardware fasteners. This most basic finish can be used when protection is not an issue or indoors. This finish is susceptible to rusting and corrosion in exterior environments. Often the surface has been oiled which improves lubricity. Nothing has been done to this bare metal surface to improve appearance or corrosion resistance, which is very low if the material is steel.
